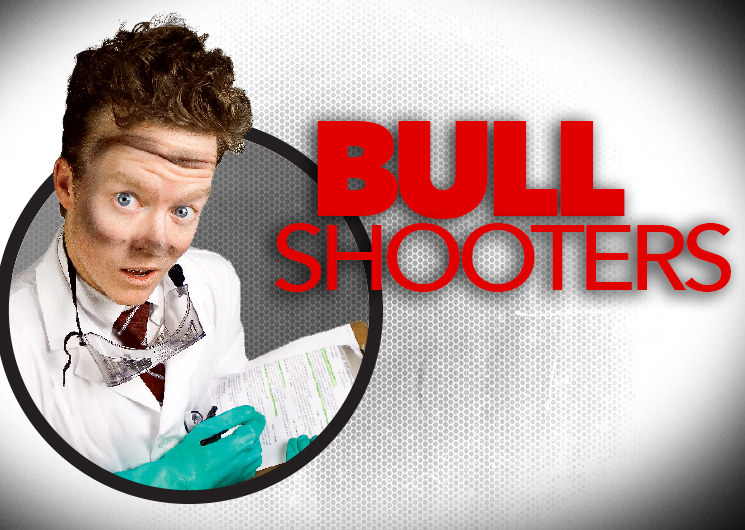
Part 3 of10
Some assembly required
With a box of parts that were light enough to carry in my pocket, I loaded up and headed to the machine shop. The goal was to assemble the barrel and action with everything square and concentric. Tight tolerances require hand machine work and lots of time, but the payoff comes in the shape of tiny little groups on the range and confidence in the field.
Since this blog is all about experimenting and learning, the guys at Tactical Rifles, Inc., agreed to let me do some of the machine work (under VERY close supervision). They don’t offer their services commercially for partial projects, but being a big-time writer can open doors. After they stopped laughing at the size of my barrel, they put me to work. Along the way, we inadvertently busted another myth: that anyone with the right tools can build a precision rifle. We learned that lawyers should stay away from the shop.
Now down to business. After complete disassembly, the action must be blueprinted.
“Blueprinting” is shorthand for making sure all of the surfaces are square and concentric and that the threads are clean.
We start by squaring the receiver in the lathe. We cut just enough of the face off to get a perfectly square surface for the recoil lug and barrel to rest.
Truing the locking lugs ensures that they are square. The ring around the bolt is evidence of this process.
Among other hocus pocus, we true the face of the bolt to provide a square surface for the cartridge to meet.
When you demand accuracy, you simply must start with a premium barrel. Krieger’s barrels are among the best, with tight tolerances and mirror-lapped bores.
Taking accurate measurements is a key part of this process, here we determine how deep we’ll need the barrel to extend into the action.
We’ll start by cutting the threads so that they perfectly match those on the receiver. This is when I got a reminder as to why gunmakers are in business. I had just asked Tactical Rifles' Production Manager Matt Delura “Have you ever ruined a barrel?” when I made a false move with the cutter and nearly ruined the threads. Matt moved me away from the lathe without invoking any reference to my heritage or occupation, and fixed my near-catastrophic mistake. Buying two barrels for one rifle is a sure way to drive up the cost.
Now we use the .260 Remington reamer to cut the chamber. We use a set of go/no-go gauges to tell us when we’re there.
No rifle will be accurate without a good crown, we use the lathe to cut a precise target crown.
Everything is now square, true, concentric and clean—ready for assembly.
An action wrench is used to torque the barrel into place. Yep, it just screws in.
That’s it for machine work.