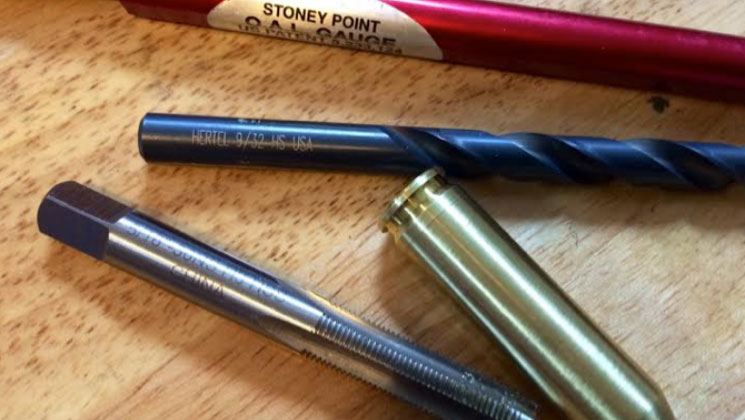
The Key Handloading Accessory
A key step of careful handloading is to determine the ideal overall cartridge length (OAL) for your particular load. Not only can seating the bullet close to the lands produce greater accuracy, but it can effectively increase the case capacity of your cartridge, which allows for lower operating pressure, all other things being equal. There are several tools on the market for determining OAL, but the Hornady tool is my personal favorite.
How It Works
The Hornady tool (mine is old enough that it was made by Stoney Point) uses modified cartridge cases that thread onto an aluminum tube. You place your selected bullet into the case, slide the cartridge into the rifle’s chamber and push forward on a rod that runs through the tube’s interior. This rod pushes the bullet forward until it contacts the lands of the rifling, at which point you lock the rod into position with a small knob. Once you retract the tool, you can measure the length of the cartridge an immediately determine in the OAL to the lands with that particular bullet—it is simple and brilliant.
The Modified Case
Hornady offers a pile of cases in various cartridges (most are $6 or $7) and, if one is not available, they will modify your case for use with the tool for $15, shipping included. But if you have a pile of tools lying around like we do, why pay someone to do what you can do yourself?
Adapting Your Own
I set out to adapt my own cases for use with the OAL tool. The case needs to be deprimed, drilled-out and tapped to the correct thread pattern. To do this yourself, you’ll need a way to hold the case while you drill and tap it, a way to deprime the case and the correct drill bit and tap.
I began with a fired case for two reasons: First, the bullet needs to be able to slide freely into and out of the case neck; secondly, I wanted the case to fit perfectly in my chamber so the measurements would be as precise as possible. I deprimed the case using a Lee depriming die which pops the primer without disturbing the case dimensions. I then placed the case into the 3-jaw chuck of my lathe, applying enough tension to hold the case without crushing it.
Using a 9/32 drill bit at low RPM, I drilled the back of the case to the proper size to fit the OAL tool.
It is crucial that the hole be drilled perfectly straight, and that the threads are aligned with the bore of the hole. In order to accomplish this, I used my lathe’s “center” to position the tap wrench.
Using tapping oil and cutting slowly, the 5/16-36” threads were cut on the case.
Once the threads were cut, the modified case threaded perfectly onto the tool.