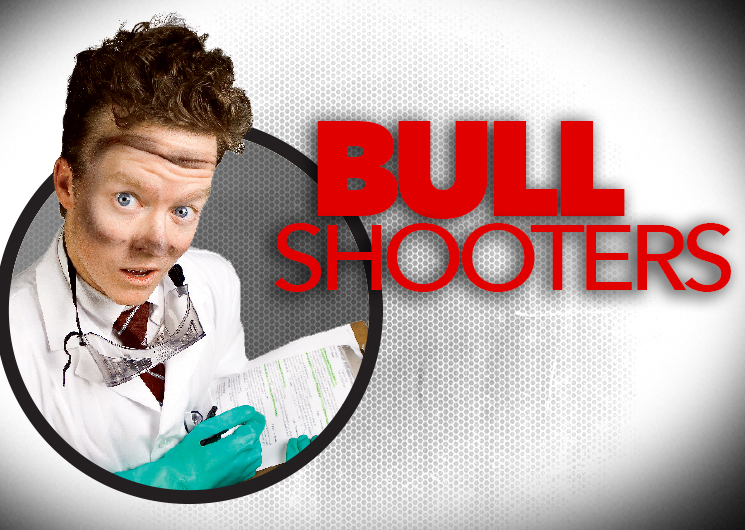
Rust Bluing: Is it really the gun finish for the hobbyist?
The Background
I’ve read for years that rust bluing, while time-consuming and tedious, is the perfect firearms finishing method for the hobbyist as it requires little in the way of special equipment. As we found out a while back, charcoal bluing isn’t as easy as it is often advertised to be—so how tough it is to rust blue steel at home?
The Equipment
Setups can vary from the Spartan to the elaborate but basically you need (all of this is available from Brownells):
- A heat source capable of boiling water
- Rust bluing solution
- A fine wire brush, wire wheel, or steel wool
- Sandpaper (if polishing is needed)
- A degreasing agent
- Vinyl, cloth, or rubber gloves
- Cotton balls or patches
- A container for boiling water large enough to accommodate the parts that you wish to blue
- Mild steel wire
- Clean water
The Theory
Essentially, rust bluing uses an acid solution to rust the steel in a controlled environment. Boiling the rust converts the red oxide to black oxide which constitutes the metal finish. The excess rust is removed and the process is repeated until the desired finish is required. This is a traditional process that is still used on high-dollar custom rifles and shotguns.
The Test
Instead of ruining a serviceable firearm, I decided to start with a bar of 4140 steel to test both the process and my abilities. I gave the steel a cursory polishing to 400 grit (bluing doesn’t “hide” any blemishes so a good polish is crucial on a real project) and gathered my materials. Brownells sent me a steel bluing tank, a carding brush, and a few bottles of solution to try. I ended up using Laurel Mountain Brown & Degreaser Solution as it contains its own degreasing agent and has a reputation for ease of use.
The first step was to degrease the steel and my wire brush—any traces of oil or grease will show up on the final finish. Remember that oil can seep out of receiver threads, crew holes, etc. Wearing gloves, I boiled the steel in detergent and then swabbed it in acetone. From this point forward, I did not touch the steel with my bare hands.
The solution is applied very sparingly (I used a cotton bore patch) in long, even strokes—don’t scrub! The metal is then allowed to rust for about three hours—this is going to depend on factors such as humidity.
In some climates, you may need to use a “sweat box” or hang the steel in a bathroom. My entire state is a sweat box so that was not necessary for me. A coat of red rust will form, and for once in your life this is a good thing. After three or so hours, re-coat the steel with solution.
It’s time to convert that rust before it pits the metal, so crank up your heat source (I used my barbecue grill—very sophisticated) and bring the water to a boil.
Use the steel wire to suspend the parts into the boiling water (do I need to tell you to be careful?).
This is where I ran into some trouble: Many sources (including the instructions on one of the solutions) tell you to use distilled water for the boiling. I bought several gallons of the Crystal brand of distilled water and boiled, and boiled and boiled. I could not get the red rust to turn black. I scrubbed my tank, I boiled for more time, I tried a different tank—nothing worked.
Finally, a gunsmith online suggested that I try a different water source. I used the water that is expelled from my home’s A/C unit and the rust turned black in seconds. Find a source of water that works for you but don’t be afraid to experiment with different sources to find the right one.
Looking for more on rust bluing? Check out the following article
• Rust Bluing: Can You Do It At Home? Part II